供异型钢高裂纹敏感铸坯质量控制研究与实践
来源:2019全国高效连铸应用技术及铸坯质量控制研讨会论文集|浏览:次|评论:0条 [收藏] [评论]
供异型钢高裂纹敏感铸坯质量控制研究与实践张学民 李长新(山东钢铁集团研究院 山东 济南 250101)摘 要:为提升异型钢铸坯质量,莱钢炼钢厂通过原料低硫控制技术、连铸结晶器工艺优化等…
供异型钢高裂纹敏感铸坯质量控制研究与实践
张学民 李长新
(山东钢铁集团研究院 山东 济南 250101)
摘 要:为提升异型钢铸坯质量,莱钢炼钢厂通过原料低硫控制技术、连铸结晶器工艺优化等技术研究与创新,开发出供异型钢高裂纹敏感铸坯质量控制研究工艺。该工艺开发与应用,实现异型钢铸坯质量本质化稳定,而且生产成本和工序能耗得到有效降低。张学民 李长新
(山东钢铁集团研究院 山东 济南 250101)
关键词:高裂纹敏感铸坯 结晶器
Research and Practice on quality control of high crack sensitive billet for special-shaped steel
Zhang Xuemin, Li Changxin
(Shandong Iron and Steel Group Research Institute Shandong Jinan 250101)
Abstract: in order to improve the quality of special-shaped steel billets, the research and innovation of low sulfur control technology of raw materials and continuous casting mold process optimization were carried out in Laigang steelmaking plant. The development and application of this technology can realize the stable quality of special-shaped steel billet, and reduce the production cost and process energy consumption effectively.
Key words: high crack sensitive billet mould
1 前言
山钢股份莱芜分公司异型钢生产线的投产,标志着莱钢型钢产线实现型钢产品规格全覆盖,大幅提升了莱钢型钢产品竞争力,但由于异型钢轧制工艺与常规轧制不同,易出现轧制裂纹及轧材性能不达标现象,而且莱钢异型钢铸坯由原中型型钢线生产,由于原炼钢工序设备工艺落后,铸坯质量稳定性差,导致异型钢产品性能及产品表面质量波动;优化及提升炼钢工序控制水平是异型钢铸坯质量提升关键,对稳定异型钢产品质量,实现莱钢精品强企战略意义重大。
1.1 生产线主要概况
主要流程:喷镁脱硫——顶(复)吹转炉——LF(吹氩)——连铸机
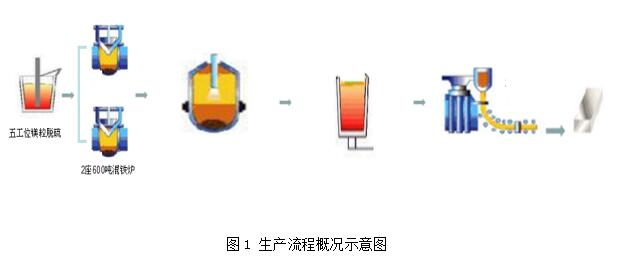
1.2存在的主要问题
异型钢钢种成分硫、磷含量较原生产线生产常规钢种低,炼钢工序为保证产品成分达标,采用延长后吹等措施进行调整,导致铸坯成分稳定性差、氧含量高;由于铸机设备工艺参数及浇注工艺与钢种需求匹配性差,导致铸坯表面及内部质量较差,影响轧材质量提升。
2 入炉原料低硫控制技术
硫在钢中偏析严重,它以熔点较低的FeS形式存在,单独存在的FeS的熔点只有1190℃,而在钢中与铁形成共晶体的共晶温度更低,只有988℃,当钢凝固时,硫化铁析集在原生晶界处,是铸坯出现表面裂纹的主要原因之一。而且在1100~1200℃进行轧制时,晶界上的FeS就将熔化,大大的削弱了晶粒之间的结合力,导致钢的热脆现象,因此对硫应严加控制。
2.1脱硫站吹气赶渣技术
在铁水脱硫处理后,在扒渣工位将铁水包顶起,然后利用机械装置将吹气赶渣枪放入铁水包内,利用枪内喷出气体的涌动作用将铁水渣聚集在铁水包的下半圆,然后集中对下半圆进行扒渣处理,提高铁水扒渣效果,减少冶炼过程回硫量(图2)。
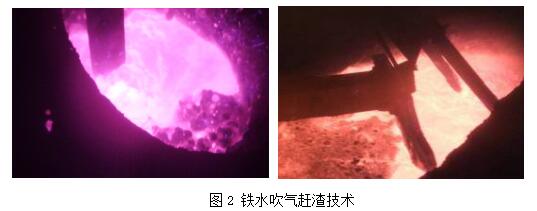
2.2混铁炉炉渣控硫技术
由于老区铁水脱硫设备及工艺落后,铁水硫含量稳定性不高,经常出现转炉入炉铁水硫含量上限炉次,若铁水带渣量超标,转炉在冶炼过程中,铁水渣回硫量大,会导致终点钢水硫含量上限或超标,影响铸坯质量稳定,通过在混铁炉实施炉渣控硫技术,可避免铁水渣回硫情况出现,技术要点如下:根据冶炼钢种硫含量设定混铁炉控硫值,铁水硫含量值到达控硫值(表1),通过混铁炉调温等措施将铁水渣进行固化,减少铁水包铁水带渣量,杜绝转炉冶炼过程回硫量大的情况出现,当混铁炉硫含量达到解除固渣硫含量值时,通过提高混铁炉炉温等方式,将混铁炉炉渣融化并及时排除,避免混铁炉积渣过量影响正常运行。
表1混铁炉固渣工艺参数表
钢中硫含量要求,% | 固渣硫含量值,% | 混铁炉固渣炉温控制值,% | 解除固渣硫含量值 | 混铁炉解除固渣炉温控制值,% |
0.04 | 0.035 | 1260 | 0.03 | 1280 |
0.035 | 0.03 | 1250 | 0.025 | 1280 |
0.03 | 0.025 | 1240 | 0.02 | 1280 |
2.3废钢精细化控制
由于各类废钢硫含量及夹杂不同,会对转炉操作造成一定影响,特别是化工类废钢及高硫废钢,加入转炉内会导致转炉终点钢水硫含量超标,对生产稳定和铸坯质量影响较大。为稳定转炉操作和提高铸坯质量,炼钢厂在国内率先进行了高标准的废钢分类存在及计量改造,实现入炉废钢数量及结构精准控制,避免因废钢影响转炉终点硫含量情况出现。
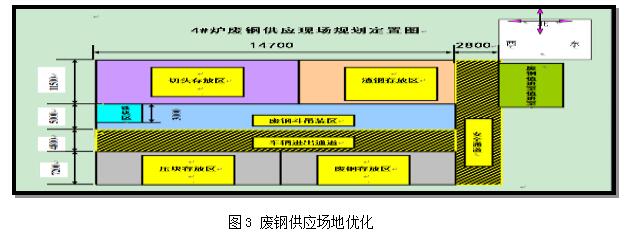
3连铸结晶器工艺优化
3.1倒角结晶器工艺
铸坯坯壳不均匀容易引起凹陷和纵裂,铸坯中间纵裂主要是坯壳不均匀和水口处的保护渣熔化和下滑不良,使坯壳温度增高所致,直角结晶器由于铸坯角部与其他位置冷却值不同,是导致铸坯坯壳不均匀的主要原因,而且钢水在结晶器角部易产生流场死角,成为夹杂的聚集地中,影响铸坯质量稳定性。通过设计采用倒角结晶器较好解决以上问题,计算出各种角度时倒角板坯角部温度变化情况如表2和图4 所示;由此可见,倒角30°时能够较好地满足既要提高角部温度避开低塑性区,又要防止角部温度高导致纵裂纹漏钢的要求。
表2 各种倒角角度的板坯角部温度变化情况
位置 | 0° | 22° | 30° | 45° |
结晶器出口处角部温度(℃) | 984 | 1147 | 1206 | 1271.7 |
离弯月面3m处角部温度(℃) | 768 | 888 | 965 | 1027 |
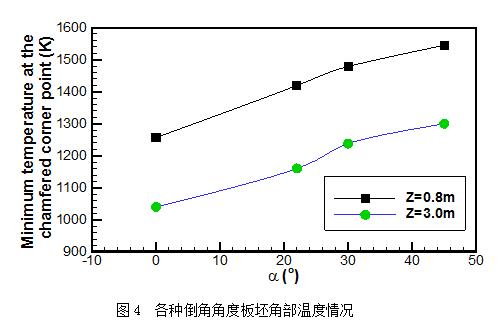
在4号铸机240 mm×375mm断面上进行倒角结晶器试验,总共5炉含钒、硼元素低合金钢。在线观察热坯表面质量,未见异常;冷坯清理,发现1支铸坯存在皮下裂纹,皮下裂纹率3.2%。对铸坯角部进行火焰抽查,未见裂纹及其他缺陷,铸坯表面原始合格率96.77%。
3.2开发“缓冷型”低耗量保护渣
根据异型钢钢种成分设计存在两大特点: [C]含量处于亚包晶区,铸坯凝固收缩量大;微合金元素种类多,含有钒、铌、硼等裂纹敏感性强元素。钢种发生包晶反应时,铸坯收缩量大,保护渣液渣的流人易出现沟槽,致使凝固收缩和传热不均,加上钒、铌、硼等裂纹敏感性强元素作用,从而容易导致铸坯表面的微裂纹产生。为避免产生皮下裂纹,保护渣设计的重点应放在控制从铸坯传往结晶器的热流,限制结晶器热通量,提高液渣流入均匀性。
“缓冷型”低耗量保护渣优化如下:高碱度,保护渣的碱度越高,凝固温度、析晶温度就越高,提高渣析晶比率和固渣膜的厚度,增加铸坯和铜管壁之间的热阻,使保护渣传热速度减缓。合适的粘度,结晶器保护渣渣膜的厚度和均匀性与粘度有很大的关系,粘度过低会使渣膜增厚,且不均匀,铸坯由于冷却的不均匀,易产生裂纹,粘度过高,又会使液渣流人困难,渣膜变薄,渣的流动性能变差。
原Q390P钢种保护渣化学成分与理化性能见表3:
表3保护渣化学成分与理化性能
SiO2 | CaO | Al2O3 | MgO | Fe2O3 | TC | 碱度 | 熔点(℃) | 粘度(Pa.S) |
29.49 | 27.63 | 9.84 | 2.02 | 2.69 | 14.28 | 0.94 | 1210 | 0.75 |
表4保护渣化学成分与理化性能
SiO2 | CaO | Al2O3 | MgO | Na2O | TC | 碱度 | 熔点(℃) | 粘度(Pa.S) |
29.70 | 38.70 | 6.80 | 1.80 | 2.30 | 13.70 | 1.30 | 1190 | 0.55 |
3.3非连续式正反向结晶器电磁搅拌技术
为了研究不同结晶器电磁搅拌参数设置对铸坯内部质量的影响,对铸坯进行取样验证,制定了试验方案,试验结果见表5、6。
表5向搅拌模式试验结果统计
方案 | 电流/A | 频率/Hz | 结晶器液面状况 | 内部质量状况 | 中心等轴晶率 |
方案1 | 200 | 2.0 | 无明显变化,±3mm | 无明显变化 | 无明显变化,22% |
方案2 | 200 | 2.5 | 无明显变化,±3mm | 无明显变化 | 无明显变化,22% |
方案3 | 200 | 3.0 | 无明显变化,±3mm | 无明显变化 | 无明显变化,22% |
方案4 | 300 | 2.0 | 无明显变化,±3mm | 中间裂纹、中心裂纹 有所改善 |
有所改善,26% |
方案5 | 300 | 2.5 | 无明显变化,±3mm | 中间裂纹、中心裂纹 有所改善 |
有所改善,24% |
方案6 | 300 | 3.0 | 无明显变化,±3mm | 中间裂纹、中心裂纹 有所改善 |
有所改善,24% |
方案7 | 400 | 2.0 | 液面波动变大,±4mm | 无中间裂纹、中心裂纹 | 明显改善,32% |
方案8 | 400 | 2.5 | 无明显变化,±3mm | 无中间裂纹、中心裂纹 | 明显改善,30% |
方案9 | 400 | 3.0 | 无明显变化,±3mm | 无中间裂纹、中心裂纹 | 明显改善,29% |
方案10 | 500 | 2.0 | 液面波动变大,±6mm | 无中间裂纹、中心裂纹 | 显著提高,38% |
方案11 | 500 | 2.5 | 液面波动变大,±5mm | 无中间裂纹、中心裂纹 | 显著提高,35% |
方案12 | 500 | 3.0 | 液面波动变大,±5mm | 无中间裂纹、中心裂纹 | 显著提高,36% |
表6反向搅拌模式试验结果统计
方案 | 正转、反 转时间/s |
间歇时 间/s |
电流 /A |
频率 /Hz |
结晶器液面 状况 |
内部质量状况 | 中心等 轴晶率 |
方案1 | 10 | 3 | 350 | 2.5 | 无明显变化, ±3mm |
无裂纹,边部 轻微白亮带 |
明显改善, 34% |
方案2 | 20 | 3 | 350 | 2.5 | 无明显变化, ±3mm |
无裂纹,边部 轻微白亮带 |
明显改善, 36% |
方案3 | 30 | 3 | 350 | 2.5 | 无明显变化, ±3mm |
无裂纹,边部 轻微白亮带 |
明显改善, 35% |
方案4 | 10 | 3 | 400 | 2.5 | 液面波动变大, ±5mm |
无裂纹,边部 较大白亮带 |
显著提高, 38% |
方案5 | 20 | 3 | 400 | 2.5 | 液面波动变大, ±4mm |
无裂纹,边部 较大白亮带 |
显著提高, 37% |
方案6 | 30 | 3 | 400 | 2.5 | 液面波动变大, ±4mm |
无裂纹,边部 较大白亮带 |
显著提高, 38% |
方案7 | 10 | 3 | 450 | 2.5 | 液面波动明显, ±6mm |
无裂纹,边部 白亮带明显 |
显著提高, 40% |
方案8 | 20 | 3 | 450 | 2.5 | 液面波动明显, ±6mm |
无裂纹,边部 白亮带明显 |
显著提高, 38% |
方案9 | 30 | 3 | 450 | 2.5 | 液面波动明显, ±6mm |
无裂纹,边部 白亮带明显 |
显著提高, 39% |
表7器电磁搅拌参数设置
断面 | 模式 | 正转、反转时间 | 间歇时间 | 电流 | 频率 |
240*375断面 | 正反向 | 20s | 3s | 350A | 2.5Hz |
275*380断面 | 正反向 | 20s | 3s | 365A | 2.5Hz |
320*410断面 | 正反向 | 20s | 3s | 390A | 2.5Hz |
在实际生产中,选择振动参数时不仅要考虑钢种和拉速,还应考虑到保护渣的作用。特别是振幅、频率及负滑脱比等参数,因为这些参数对保护渣的耗量和润滑性能有较大影响。如果选择不当,使铸坯产生大量缺陷,严重时引起漏钢。
负滑脱时间对结晶器振动冶金效果的正负两方面的影响效果,一方面负滑脱时间长有利于“压合”效果以及使铸坯表面的振痕变浅,另一方面保护渣沿坯壳与结晶器壁之间的渗入量则随着负滑脱时间的增加而减少,不利于铸坯润滑和结晶器传热。对于包晶钢等裂纹敏感性强的钢种,对应的负滑脱时间目标值即应取得相对小一些,以改善润滑、传热条件。
新设计分阶段恒振频控制模型:
S=C1+C2*Vc
f=C3+C4*Vc+C5*Vc/(2*S)
式中 S—振程,mm
Vc—铸坯拉速,m/min
f—振动频率,次/min
C1、C2、C3、C4、C5—系数
改造前传统振动模型振动参数、改造后变振幅振动模型振动参数见表8、9
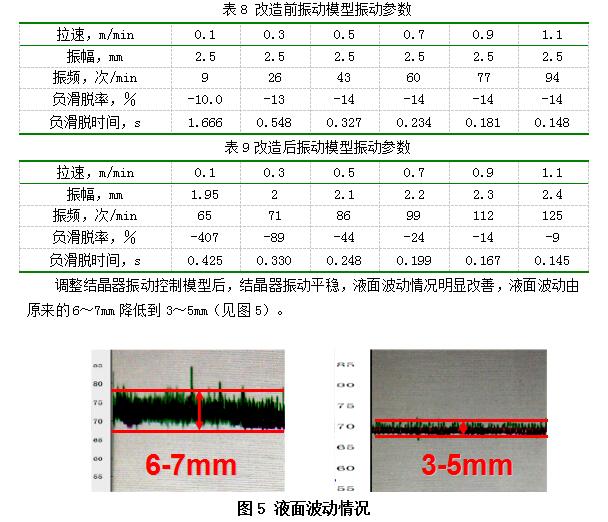
4 实施效果
4.1铸坯成分均质化得到有效提升,轧材质量实现本质化稳定
铁水吹气赶渣、混铁炉炉渣固化技术和入炉废钢精准控制,入炉硫总量降低明显,钢水硫含量降低0.005%;实现钢水成分精准控制,钢中碳、锰元素cpk分别提高0.47和0.46;出钢紊流工艺和结晶器电磁搅拌技术实施,使铸坯均质化程度得到提升,铸坯及轧材质量得到有效提升。
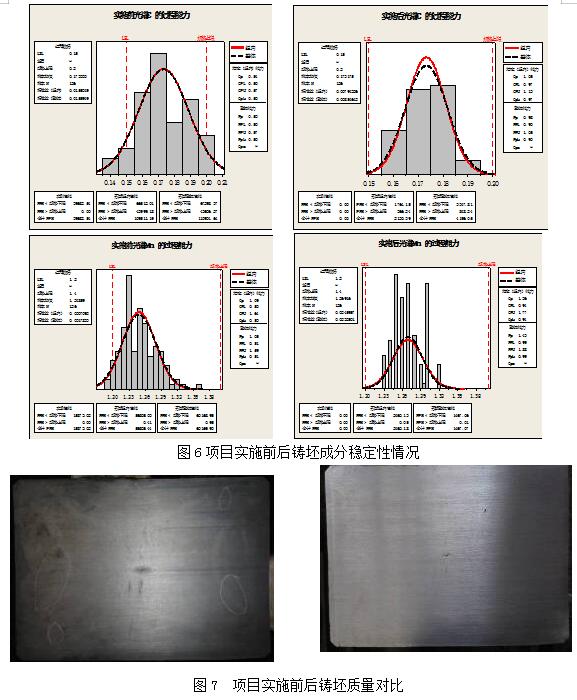
4.2经济和社会效益显著
异型钢铸坯质量控制工艺实施,钢水氧化性得到降低,脱氧剂及合金加入量减少,吨钢成本降低1.74元/t钢;铸坯质量本质化稳定,实现异型钢批量生产,产能及品种创效能力明显增强;实现高效低能耗冶炼,为企业绿色发展奠定基础。
参考文献:
[1] 杜辰伟,兰鹏,汪春雷,张家泉,等.微合金钢连铸坯表面裂纹敏感性预测模型[J].中国冶金,China Metallurgy,2019年07期
[2] 刘军.微合金钢铸坯角部横裂纹控制技术的应用[J]. 连铸,Continuous Casting,2019年03期
延伸阅读
- 上一篇:河钢承钢2500m3高炉配加澳球的实践 下一篇:韶钢8号炉提煤降焦操作实践