特殊钢大方坯连铸末端电搅和软压下优化组合
浏览:次|评论:0条 [收藏] [评论]
特殊钢大方坯连铸末端电搅和软压下优化组合Coordinating optimisation of F-EMS and soft reduction during bloom continuous casting process for special steel摘 录:大方…
特殊钢大方坯连铸末端电搅和软压下优化组合
Coordinating optimisation of F-EMS and soft reduction during bloom continuous casting process for special steel
Coordinating optimisation of F-EMS and soft reduction during bloom continuous casting process for special steel
摘 录:大方坯连铸过程中控制中间裂纹和缩孔,需要优化末端电磁搅拌和软压下技术,采用下面的技术就能够成功地控制中间裂纹和缩孔:(1)控制连铸拉速为 0.62m/min,(2)二冷比水量为 0.2L/kg,(3)软压下总量为 18mm;(4)压下范围从距离弯月面 19.9m(第三台拉矫机)一直到 25.4m(第 9 架拉矫机);(5)对应的拉矫机辊子压下分配为 1,1,2,3,4,4,和 3mm,对比原先生产轴承钢的工艺参数,通过优化方案,铸坯中心碳偏析最大值和最小值之差从 0.35 降低到 0.09。
介绍
目前,高等级特殊钢使用大方坯连铸机生产,这样可以改善产品的质量[1,2],比如轴承钢,弹簧钢和易切削钢。大断面特殊钢铸坯的中心疏松和缩孔与宏观偏析对应,所以铸坯的疏松和缩孔对于后续锻造和轧制工序来说就是质量瓶颈[3],于是,较好的理解中心宏观偏析控制技术对于提高特殊钢内在质量意义重大。
为了改善连铸坯内在质量,采用了一系列技术,如低温浇铸[4],在最后的凝固阶段采用结晶器电磁搅拌[5,6],软压下[7,8],强化二冷[9]等措施,在这些技术措施中,末端电搅和软压下技术广泛使用,证明是可以有效地增加轧制铸坯的成分和组织的均匀性[10~12]。然而,单独采用末端电搅或者软压下技术,总是感觉到对控制产品质量还存在不足,比如使用末端电磁搅拌技术对等轴晶细化和扩大等轴晶区有利,但是对最终的凝固阶段体积上的收缩造成的疏松和缩孔无能为力[12,13],单独使用软压下技术,在最后凝固体积收缩阶段,无法扩大铸坯内部等轴晶率[14,15]。
建立在上面的讨论,对现场基本半径为 12 米连铸机生产轴承钢 GCr15 采用末端电搅和软压下优化组合,该连铸机弧线上布置有 5 台独立拉矫机,中国韶关钢厂的铸机装备有结晶器电磁搅拌(M-EMS),末端电磁搅拌(F-EMS)和软下压功能。生产中采用酸洗低倍观察低倍试样,使用湿法分析观察铸坯宏观成分偏析。z
背景
表 1 给出连铸生产 GCr15 轴承钢主要工艺参数,表 2 给出工业化生产轴承钢的化学成分和目标值,表 3 给出拉矫机位置和对应的压下量分配。为了得到准确的压下量参数,拉矫机上辊压下液压缸内位移传感器给出信号,拉矫机下辊固定不变,图 1 显示了典型的轴承钢GCr15 纵向低倍组织,其铸坯的连铸参数见表 1。从低倍看中间缩孔间断分布,看到 34mm 长度的中间裂纹,其裂纹从铸坯的内弧表面 80mm 开始到 114mm 地方结束,图 2 给出这个中间裂纹的厚度方向上的高倍照片,图 3 给出了位于图 2 中裂纹的扫描电镜照片,可以看到在裂纹 1、2 和 3 内部的表面有大量的树枝晶结构,将其归类于局部的枝间宏观偏析和疏松[15],图 2 中裂纹 4 内部平滑的表面表示裂纹终端,这是由于不恰当的压下量不足引起局部熔融金属被抽吸形成的空腔,图 4 给出来这种现象形成的图 1 中间缩孔扫描电镜照片,可以看见许多柱状晶在空腔内部,说明表 3 中列出的软压下参数并不能有效的补偿最终阶段出现的体积上的收缩[18,19],建立在上述的讨论,说明了现有的末端电磁搅拌和软压下参数并不能满足高质量铸坯的要求。
表 1 原先 GCr15 轴承钢连铸工艺参数
参数 | 数值 | 参数 | 数值 |
铸坯断面 | 320x425mm | 拉速 | 0.62m/min |
过热度 | 25~35℃ | 结晶器搅拌器电流 | 700A/2.5Hz |
总压下量 | 18mm | 末端搅拌器电流 | 600A/5Hz |
二冷比水量 | 0.26L/kg | 末端搅拌器线圈位置 | 距离弯月面 15.05m |
C | Si | Mn | P | S | Cr | Cu | |
控制范围 | 0.96~1.03 | 0.17~0.25 | 0.32~0.39 | ≤0.015 | ≤0.010 | 1.45~1.52 | ≤0.15 |
目标值 | 0.99 | 0.2 | 0.35 | ≤0.01 | ≤0.005 | 1.48 | ≤0.15 |
M1 | M2 | M3 | M4 | M5 | M6 | M7 | M8 | M9 | |
压下分配 | 0 | 2 | 3 | 4 | 4 | 3 | 2 | 0 | 0 |
距离弯月面 | 17.7 | 18.8 | 19.9 | 21.0 | 22.1 | 23.2 | 23.3 | 24.3 | 25.4 |
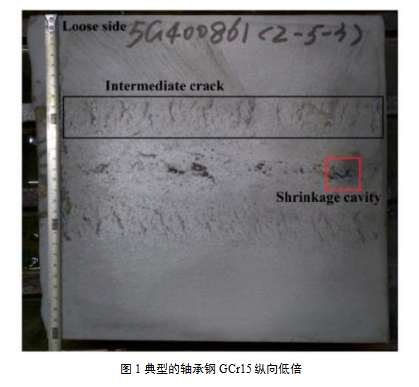
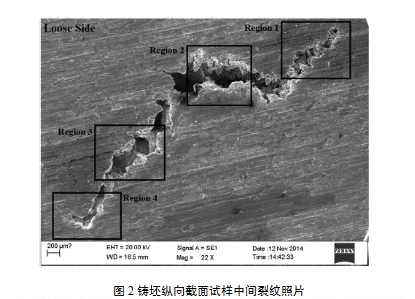
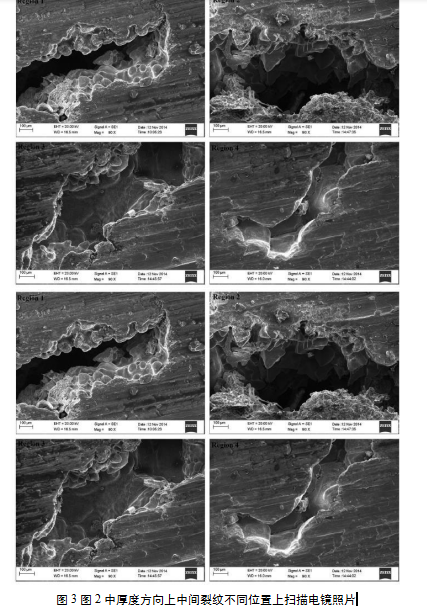
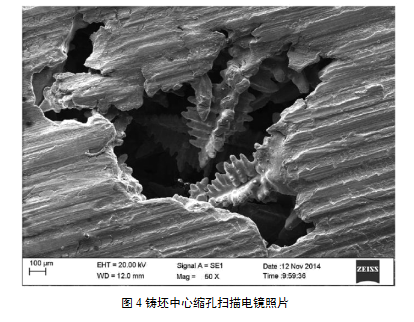
优化末端电磁搅拌和软压下
传热和凝固行为
为了精确地评价对末端电磁搅拌和软压下优化技术,研发了耦合传热过程和凝固行为的 2D 瞬态数学模型,图 5 给出了二维耦合模型的网格划分和边界条件,其数学描述可以见 Zhu 团队[13]和 Ji 团队[14]发表的文献,图 6 显示了模拟和实测的铸坯宽面中心沿着连铸方向坯壳厚度和温度变化,其生产轴承钢连铸机参数见表 1,沿着拉坯方向铸坯中心的固相率也表明在图 6a 中,在这些中,铸坯表面温度测量在线使用红外高温仪,测量位置在距离弯月面 4.4m,8.25m,13.35m,14.25m,16.5m 和 18.2m,射钉位置为距离弯月面 17.2m 和 22.6m 上。
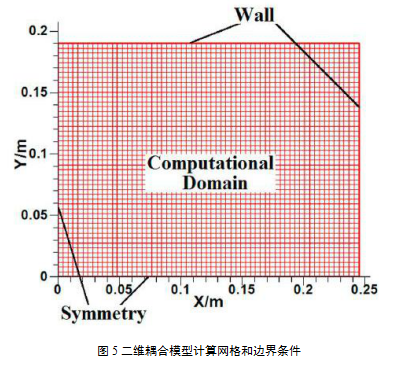
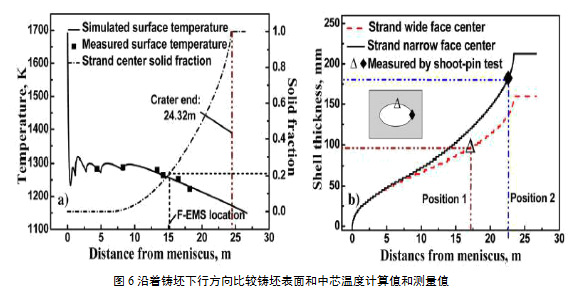
从图 6 中看出模拟计算的结果与实测非常吻合,在射钉位置上的铸坯宽面中心温度和坯壳厚度,其计算和实测误差为 15℃和 6mm,然而,在图 5a 观察到凝固末端位于从弯月面开始的 24.32m,铸坯中心固相率 fs 在末端电磁搅拌(F-EMS)线圈中心是 0.21,这个数值是大于优化的固相率范围的(0.1<fs<0.2),优化的固相率范围是 Ayata 团队建议的[20]。可以这样认为当前的 F-EMS 线圈安装位置对于 GCr15 轴承钢并非最佳位置。
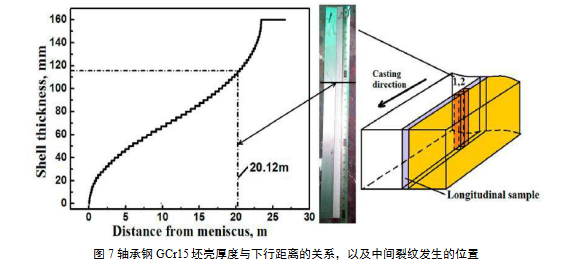
图 7 给出中间裂纹起始位置和坯壳厚度与下行距离的关系,生产轴承钢连铸参数见表1 所示,试样 1 和试验 2 尺寸为 20mmx20mmx160mm,可以看见中间裂纹开始出现在弯月面下面约 20.12m 的距离上,对于轴承钢 GCr15 来说,在拉矫机 M2,M3 和 M4 给出的压下量过大,这些压下参数见表 3.
优化组合和钢厂试验
按照上述的讨论,在末端搅拌线圈位置上的固相率在拉速不变的情况下,随着二冷强度改变而变化,图 8 表示的是在 0.26L/kg 和 0.20L/kg 两种比水量铸坯不同位置上的固相率,降低二冷比水量从 0.26L/kg 到 0.20L/kg,可以看出在末端电搅线圈位置上中心液相穴的固相率从 0.21 降低到 0.18,凝固末端从 24.32m 增加到 25.87m。
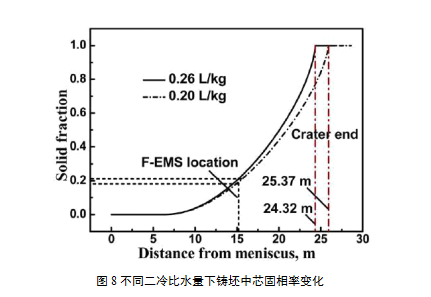
然而,要改善和消除轴承钢的中间裂纹,当二冷比水量降低到 0.2L/kg 时候,前三架拉矫机的压下必须减弱,凝固末端的压下范围需要增加,表4 给出了详细的末端电磁搅拌和软压下试验参数。
表4 新的末端搅拌和软压下试验方案
拉速 m/min |
比水量L/kg | 压下总量 mm |
M1 | M2 | M3 | M4 | M5 | M6 | M7 | M8 | M9 | |
原先 | 0.62 | 0.26 | 18 | 0 | 2 | 3 | 4 | 4 | 3 | 2 | 0 | 0 |
1 | 0.62 | 0.20 | 18 | 0 | 0 | 2 | 3 | 4 | 4 | 3 | 2 | 0 |
2 | 0.62 | 0.20 | 18 | 0 | 0 | 1 | 2 | 2 | 3 | 4 | 4 | 2 |
3 | 0.62 | 0.20 | 18 | 0 | 0 | 1 | 1 | 2 | 3 | 4 | 4 | 2 |
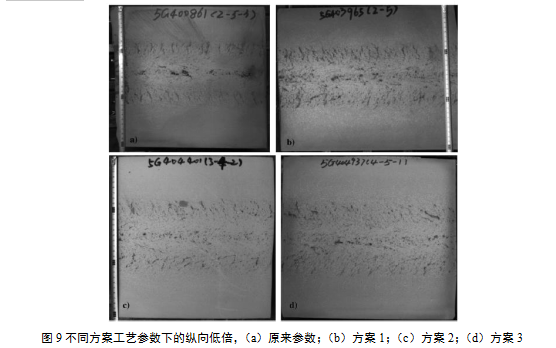
然而,对比方案 1,方案 2 和方案 3 低倍中的中间裂纹和中心缩孔几乎消失,这是减小了前面三架拉矫机的压下量(M3-M5),避免了中间裂纹的产生,而在最后三架拉矫机(M7~M9)增加了压下量,从而低倍组织得到完好的效果。
进而定量看表 4 中几个方案的铸坯内在质量,图 10 给出了溶质元素碳的宏观偏析,这是在纵向中心取样分析的结果,偏析程度是取样点成分与熔炼分析的比值,在中心取样点的间距为 10mm,从试样的碳偏析来看,原有方案,方案 1,方案 2,方案 3 对应的中心碳偏析最大值与最小值差分别为 0.35,0.25,0.11 和 0.09,建立在上述的结果,组合优化铸机的末端电磁搅拌和软压下技术参数,可以达到改善铸坯内在质量的目的,F_EMS 可以晶粒细化和溶质元素均匀分布,凝固末端的软压下优化改善铸坯中心缩孔。
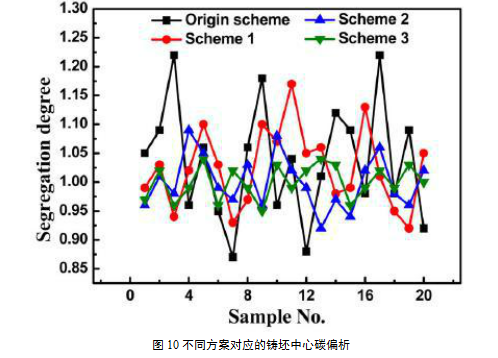
结论
通过优化组合连铸机末端电磁搅拌和凝固末端软压下工艺参数,改善了铸坯的中间裂纹,铸坯低倍质量得到提高,结论概况如下:
(i) 末端电磁搅拌参数和软压下技术参数不合理造成了铸坯的中间裂纹和缩孔形成。(ii) 对比 0.26L/kg 二冷比水量,采用 0.20L/kg 比水量后铸坯中心缩孔产不多消除。(iii) 在 320mmx425mm 矩形坯铸坯上成功采用下列技术就可以消除中间裂纹和中心缩孔:拉速为 0.62m/min,二冷过程比水量为 0.20L/kg,拉矫机 M3 到 M9 的总体压下量为 18mm,对应的压下量分配为 1,1,2,3,4,4 和 3mm。
(iv) 对比原先生产 GCr15 轴承钢方案,通过优化组合 F-EMS 和软压下工艺参数,沿着铸坯纵向中心分析的碳偏析最大值和最小值的差值从 0.35 降低到 0.09.
作者
孙海波, Liejun Li, Jinghui Wang, Xiaowen Cheng & Feng Zhou
参考文献
[1] Wang S, De Toledo GA, V?limaa K, et al. Magnetohydrodynamic phenomena, fluid control and computational modeling in the con?tinuous casting of billet and bloom. ISIJ Int. 2014;54(10):2273–2282.
[2] Sun H, Li L. Application of swirling flow nozzle and investigation of superheat dissipation casting for bloom continuous casing. Ironmak Steelmak. 2016;43(3):228–233.
[3] Sun H, Li L, Cheng X., et al. Reduction in macrosegregation on 380 mm×490 mm bloom caster equipped combination M+F-EMS by optimising casting speed. Ironmak Steelmak. 2015;42(6):439–449.
[4] Ayata K, Mori H, Taniguchi K, et al. Low superheat teeming with elec?tromagnetic stirring. ISIJ Int. 1995;35(6):680–685.
[5] Liu H, Xu M, Qiu S, et al. Numerical simulation of fluid flow in a round bloom mold with in-mold rotary electromagnetic stirring. Metall Trans B. 2012;43(6):1657–1675.
[6] Ren BZ, Chen DF, Wang HD, et al. Numerical simulation of fluid flow and solidification in bloom continuous casting mould with electro?magnetic stirring. Ironmak Steelmak. 2015;42(6):401–408.
[7] Domitner J, Wu M, Kharicha A, et al. Modeling the effects of strand surface bulging and mechanical softreduction on the macrosegrega?tion formation in steel continuous casting. Metall Trans A. 2014;45 (3):1415–1434
[8] Li X, Ding H, Tang Z, et al. Formation of internal cracks during soft reduction in rectangular bloom continuous casting. Int J Miner, Metall Mater. 2012;19(1):21–29.
[9] Ludlow V, Normanton A, Anderson A, et al. Strategy to minimize central segregation in high carbon steel grades during billet casting. Ironmak Steelmak. 2005;32(1):68–74.
[10] Ji C, Wu C, Zhu M. Thermo-mechanical behavior of the continuous casting bloom in the heavy reduction
process. JOM. 2016;68 (12):3107–3115.
[11] Li G, Yu W, Cai Q. Investigation of reduction pretreatment process for continuous casting. J Mater Process Technol. 2016;227:41–48.
[12] Zeng J, Chen W, Zhang S, et al. Development and application of final permanent magnet stirring during continuous casting of high carbon rectangular billet. ISIJ Int. 2015;55(10):2142–2149.
[13] Jiang D, Zhu M. Flow and solidification in billet continuous casting machine with dual electromagnetic stirrings of mold and the final solidification. Steel Res Int. 2015;86(9):993–1003.
[14] Ji C, Luo S, Zhu M. Analysis and application of soft reduction amount for bloom continuous casting process. ISIJ Int. 2014;54(3):504–510.
[15] Xiao C, Zhang J, Luo Y, et al. Control of macrosegregation behavior by applying final electromagnetic stirring for continuously cast high carbon steel billet. J Iron Steel Res Int. 2013;20(11):13–20.
[16] Zeng J, Chen W, Wang Q, et al. Improving inner quality in continuous casting rectangular billets: comparison between mechanical soft reduction and final electromagnetic stirring. Trans Indian Inst Met. 2016;69(8):1623– 1632.
[17] Xu Y, Xu R, Fan Z, et al. Analysis of cracking phenomena in continu?ous casting of 1Cr13 stainless steel billets with final electromagnetic stirring. Int J Miner, Metall Mater. 2016;23(5):534–541.
[18] Liu K, Sun H, Peng L, et al. FEM analysis of soft reduction amount and its internal reduction efficiency for continuous casting railway blooms. Pittsburgh: AISTech; 2013. p. 1427–1438.
[19] Elbealy MO. Macrosegregation quality criteria and mechanical soft reduction for central quality problems in continuous casting of steel. Mater Sci Appl. 2014;05(10):724–744.
[20] Ayata K, Mori T, Fujimot T, et al. Improvement of macrosegregation in continuously cast bloom and billet by electromagnetic stirring. Trans ISIJ. 1984;24(11):931–939.
唐杰民 2019 年黄山屯溪春节期间翻译自<Ironmaking & Steelmaking> 2018 VOL 45 NO. 8. 708~713
唐工阅读体会
各位老师和专家好!春节期间看了一篇有关轴承钢生产的文章,我觉得对国内生产轴承钢连铸工序是有一定的参考价值的,所以翻译出来。
文章概述
这篇文章是介绍广东韶关钢厂在 R12 米半径的连铸机上生产大断面轴承钢情况,主要是从末端电磁搅拌和软压下工艺参数优化来解决原来出现的铸坯中间裂纹和中心缩孔问题,通过几种方案的试验,分析对比,从而找出最佳的工艺参数,达到了消除中间裂纹和中心缩孔的缺陷,从而提高了轴承钢 GCr15 的内在质量。
韶关钢厂生产的是大断面矩形坯,320x425mm,如果生产较大规格的棒材,可以得到相对大的压缩比,有利于提高轴承钢棒材的内在质量。但是由于铸坯组织内部存在先天不足,选分结晶的自然属性造就了缩松和缩孔,这是凝固结晶的必然现象,产生的缩松,裂纹,缩孔和偏析等内在缺陷只能通过现代技术手段加以限制和消除,孙海波老师写的文章就是组合使用末端电磁搅拌和软下压,通过对工艺参数的优化来消除中间裂纹,细化晶粒,消除中心缩孔,减小铸坯中的碳偏析。
评价轴承钢质量
我还是坚持钢铁企业生产轴承钢的偏析和内部组织结构的评价是以轧制棒材来评定的,使用连铸坯轧制成为圆棒材,也就是生产轴承部件的原料来评价其组织和偏析,比如φ50mm棒材。铸坯横向断面和铸坯纵向出现一定程度的偏析,但是如果能够在后续的锻造或轧钢工序中克服,能够在压力加工工序中弥补其连铸过程的缺陷,交付给用户的轴承钢棒材就是较好的产品,还是用胡适先生的原句,实践是检验真理的唯一标准,轴承制造商需要的是轴承钢 GCr15 等钢种的圆棒材,而不是铸坯。
我去年翻译一篇轴承钢疲劳试验的文章,《碳化物偏析对轴承疲劳寿命的影响》选用了几家不同轴承钢制造商制造的轴承进行试验,成分都差不多,看不出来有什么区别,但是疲劳寿命相差甚远,文章指出了是微观组织上面的问题,文章放在技术群中,引起一些专家和学者的共鸣。我这里说的意思是不必要将生产的轴承钢质量水平随意拔高,轴承制造环节中的热处理,加工和装配等加工工艺也是非常重要的,对最终的轴承质量往往起到至关重要的作用。
钢水过热度
铸坯断面存在碳偏析缺陷,严重影响了轴承钢的性能指标,从目前来看在连铸工序上控制元素偏析手段基本上就是低过热度浇铸,结晶器电磁搅拌和末端电磁搅拌,软压下技术,重压下技术。我从长期的生产实践来看,过热度的影响并非像各种书籍和文章中反复强调的那样大,从非金属夹杂物的扩散脱氧来看,需要钢水具有一定的温度,才能保持钢水具有一定的黏度,给夹杂物上浮创造一定上浮条件,所谓的非常低的过热度浇铸不见得是有效的,这与电渣重熔的思想是不一样的,所以不能拿电渣重熔的原理对应连铸和模铸生产。合理的过热度我还是坚持认为是 25~40℃,对于 GCr15 轴承钢来说中间包温度保持在 1590℃左右比较合理的,从传热计算来看,几度显热误差对连铸传热影响是不大的,从实践上看,对低倍的低倍组织,碳偏析影响也不甚显著,从组织生产和控制钢中的非金属夹杂物来看,我坚持不必要苛刻地来控制钢水过热度。
全氧和钢水温度控制
轴承钢最为重要的指标之一是全氧含量,从某钢厂最近两次的实践来看,即使中间包钢水过热度看起来较高,但是氧氮分析的结果表明全氧含量约为 8ppm,考虑到使用的外装式浸入式水口,钢水吸气造成的氧含量升高估计在 2~3ppm,这样来看,如果使用组合式浸入式水口,控制氧含量的效果还是能够再提高的,基本上就能够达到均值为 6ppm 的水平上来,目前来看国内外最高水平也就是这个水平,至于说能够达到 4ppm 或者 5ppm 的宣传,那仅仅是个别炉次,不见得代表整体。
我这里说采用的钢水过热度范围较宽,这是从现有设备条件组织生产的角度上来看,轴承钢必须走真空工序,真空工序难以控制钢水温度,即使是相同的钢包寿命,相同的成分和进入温度,使用同样的抽气程序,但是出来的钢水温度还是有所差别的,我在组织生产中对于非真空钢,使用精炼炉能够达到 25±5℃控制水平,甚至能够达到 20±3℃的水平。如果经过真空炉操作,这个控制水平就要落在 30±7℃的水平上。我总是幻想一个这样的测温仪器,在真空情况下能够精确测定钢水温度,如果钢水温度过高,就多抽气一段时间,如果温度低了,不必多抽,这样就能够在一定程度上来控制钢水温度了,遗憾的是到目前为止没有看到这样的设备。我曾经和老外询问此事,西门子奥钢联都在做这个研究,他们在俄罗斯进行试验,但是其精度只能达到±20℃,这个精度对于现场组织生产是没有用的,仪器的精度必须达到±5℃才能在工业现场上使用,看来我们还是需要再等待一段时间了。
控制疏松和缩孔
某钢厂在三号连铸机上没有安装末端电磁搅拌,但是采用了奥钢联的软压下技术,采用7个单独的拉矫机按照奥钢联的软件模型分配凝固末端的压下程序,从二次的轴承钢生产情况来看,轴承钢的氧含量和碳偏析控制相对较好,我认为可以达到国内中等的水平。200mm方坯轴承钢 GCr15 铸坯质量关键为中心缩孔和疏松,由于钢厂的轧机能力不足,只能使用 200mm 方坯生产圆棒材,轧制压缩比是比较小的,铸坯中芯部位的疏松和缩孔难以完全焊合,这是影响轴承钢质量的难点,不仅仅轴承钢存在这个方面的弱项,其它品种钢棒材我想都有这样的问题。
控制铸坯的中间疏松和中心缩孔是连铸软压下和末端电磁搅拌的最为主要的工作,目前阶段是按照外方的软件来实现自动分配压下,从二次生产来看,中心缩孔现象还是存在的,有的炉号铸坯取样没有看到缩孔,但是并不能代表这个炉号的铸坯就没有中心缩孔,毕竟横向低倍的代表性不强,往往难以取到中心缩孔缺陷处,一定要以纵向低倍来评价铸坯的内在质量,只有纵向低倍最具备代表性。唐工翻译的这篇文章的亮点之一就是全部采用了纵向低倍样,希望钢厂能够解决纵向低倍的切割问题。唐工这里也指出,不必要切割过长的纵向低倍,也就是切割 200~300mm 长度的纵向低倍即可,如果要评价一定长度方向上的纵向低倍,那么就连续切割几个 300mm 长度的纵向低倍就可以代表。我希望钢厂的工程师们和领导仔细阅读体会这篇文章。
铸坯选分结晶和最后凝固阶段的收缩必然产生元素的偏析和疏松缩孔,软压下技术的采用就可以在凝固末端通过对铸坯的压下,将变形渗入到铸坯的中芯液相穴,其实简要地说,就是将疏松和缩孔通过压下的作用压合起来,从而使得铸坯成为一个连续的整体,我们一定要有这样的认识,疏松就是微缩孔,对于后续的轧钢加热过程碳扩散就是阻隔的天河,在连铸工序上压合疏松缩孔以及裂纹,对后续的轧钢加热碳扩散就创造了先决条件。虽然碳原子在高温阶段上的扩散需要很长时间,但是能够做到一定程度的扩散均匀化总比没有好,我在实践中能够体会到轧钢加热扩散作用的。
压合铸坯中芯部位的疏松和缩孔还有一层意义就是不给氢的扩散创造居所条件,我曾经反复强调这个作用,这也是软压下的重要作用之一。
针对外方的软压下功能,唐工为此了一个文件,阐述其作用,讲述了怎么样来评价软压下,我还是希望钢厂能够主动做一次铸坯在轧钢加热炉前后都取样,制作低倍和分析偏析,从而全面评价自己的产品,当然这样做是需要一定的工作量,既然成立了技术中心,就可以安排力量专门组织这次试验。唐工过去干事情有一股热情,和职工一起来干,这样就可以掌握第一手资料,我还是希望轧钢工序能够提高加热温度,并且适当延长均热时间,为碳元素的扩散均匀化创造条件,目的就是减小碳偏析。
压下位置和压下量分配
这篇文章阐述的重点就是通过改变二冷强度,延长了凝固末端位置,通过改变末端电磁搅拌线圈的位置来达到液相穴中的钢水固相率在合理优化的范围内。钢厂没有设置末端搅拌设备,所以不谈这个问题。这篇文章重点就是改变软压下位置和分配,看来达到较好的效果,从唐工理解上看,通俗的讲,就是减小前面拉矫机的压下量,将较大的压下量分配在固相率高的末端,这样做的目的就是防止缩孔的出现,同时也可以降低中间疏松的。东方特钢也是可以根据文章中的思路,改变其软压下的位置和压下分配,从而达到较为理想的低倍组织。
合同生效后的开球会上我提出来是否具备重压下功能,老外是不同意全凝固后的压下,但是我要求拉矫机具有一定的轧制压力,记得当时老外给出最大的轧制压力为 150 吨,这样就有可能对较小断面 200mm 方坯实施一定程度的较大压下,等到设备质保期过后,钢厂可以试试看这种压下,钢厂的冶金和连铸工程师要从从理论上和实践上尽可能优化操作。
如何合理分配压下量需要做长期的工作,根据钢水温度,二冷强度,结晶器电磁搅拌,钢种成分波动范围,压下位置,纵向取样分析,组织低倍判定,偏析分析等,最终产品质量的评价要根据轧制后的棒材来分析,从而给出钢厂一个完整的品种钢数据链。
唐工春节期间翻译这篇文章,感觉可能对钢厂有用,一边过年一边翻译,同时写了这份体会和看法给大家参考,希望能够对钢厂生产轴承钢和品种钢有所帮助。
目前看钢厂要建立生产轴承钢的信心,其装备水平具备条件,人员素质也在不断提高中,这个钢种并非很难,开始就是以中低档次的钢种为主,毕竟中低档次钢种需求量大,是吃饭订单,高精尖是熊掌燕窝,量少,往往只能挣得名气,但是也是不可少的。我年前到一家生产优特钢企业参观,我看了当天夜班生产订单就有 4~5 个钢种,每个钢种量都很少,只有 400 吨左右,都是需要更换中间包的,更换一个中间包对于他们 5 流中间包耐材和三大件来说就是 2 万多元,他们也认为作为一个生产优特钢企业,还是需要一定的订单量来保证生产的连续。
延伸阅读
- 上一篇:韶钢8号炉提煤降焦操作实践 下一篇:超大型钢锭的冶炼生产